The national average SIP panel cost is around $9.70 per square foot or around $310 per panel. However, the final price can vary greatly depending on the panel’s size, insulation value, and application. On average, SIPs range in cost from about $280 all the way up to $550 per panel or between $7 and $12 per square foot.
If you’re looking for a more affordable option for your shed or garage, you can find SIPs for as low as $6 per square foot, though they may not have the same level of insulation. On the other end of the price spectrum, there are panels with extra insulation and special shapes or sizes that can cost as much as $20 per square foot or more.
SIP stands for Structural Insulated Panel, and these panels are composed of an insulating foam core sandwiched between two structural skins of oriented strand board (OSB). They provide a very high R-value per inch compared to other forms of insulation, making them energy efficient and environmentally friendly.
On this page:
- Average Costs
- Cost Estimator by Size
- Other Factors That Affect Cost
- Related Services
- Pro Cost vs. DIY Cost
- Cost by Location
- Pros and Cons of SIPs
- FAQ
Average SIP Installation Costs in 2025
National Average Cost | $9.70 per sq. ft. |
Typical Price Range | $7 – $12 per sq. ft. |
Extreme Low-End Cost | $6 per sq. ft. |
Extreme High-End Cost | $20 per sq. ft. |
When it comes to the cost of SIP panels, it’s a bit hard to give an exact price without taking into account the specifics. Generally speaking, you can expect to pay around $310 on national average for the panel itself.
This cost may vary depending on several factors, such as:
- Panel size
- Panel thickness
- R-Value (thermal resistance) of the panel
- Quality and type of insulation materials used
- Manufacturer
- Labor and installation costs
Typically, the cost of SIPs will range from around $280 to $550 for a panel of standard size and insulation value. This means that the price per square foot can range from around $7 to $12 per square foot or more, depending on the specifics of your project.
For instance, an 8′ x 24′ panel with 12.25-inch thickness and an R-Value of 48 could cost you up to $2,900 or $20 per sq.ft., while a 4′ x 8′ panel with 4.6-inch thickness and an R-Value of 16 might only be $240 or around $6 per sq. ft. on average.
Since SIPs are usually manufactured off-site and pre-cut, they can be assembled quickly, and labor costs tend to be lower than traditional insulation methods. Buying in bulk is also a great way to save money, as many manufacturers offer discounts for larger orders.
Cost Estimator by SIP Panel Size
SIPs come in various sizes, usually between 4′ x 8′ to 8′ x 24′. Generally, the bigger your panel size, the pricier it is. On average, you can expect to pay anywhere from $7 to $12 per square foot for the panel alone, not including additional materials, labor, or installation fees.
If you are going for a 4′ x 8′ panel, you can anticipate spending between $224 and $385. Larger size panels such as the 8′ x 24′ might cost you up to $2,200. Here is a cost estimator based on panel size to give you an idea of expenses.
Panel Size | Typical Cost Range (Materials Only) |
4′ x 8′ | $224 – $385 |
4′ x 10’ | $280 – $480 |
4′ x 12′ | $336 – $576 |
4′ x 16′ | $448 – $768 |
4′ x 24′ | $672 – $1,152 |
8′ x 24′ | $1,344 – $2,300 |
Other Factors That Affect Cost
SIPs are known for having improved strength and insulation, which saves money in the long run. However, when it comes to cost, several factors can affect the overall price of a SIP panel project, including the thickness and R-Value of the panel.
Cost by R-Value of SIPs
The R-Value of each SIP panel determines how much insulation it provides and is correlated to the panel’s thickness and the material used. The most popular insulation used for SIPs is expanded polystyrene rigid foam (EPS), which has an R-Value of about 3.6 per inch of thickness.
On the other hand, polyurethane has a much higher R-Value of 6.8 per inch and is an ideal option if your budget allows it. SIPs range in thickness from 4.6 inches to 12.25 inches, with total R-Values ranging from 16 to 48.
Generally, a 4′ x 8′ panel with an R-value of 16 may cost up to $240, while a 48 R-Value panel may cost up to $290 on average. Prices increase by about 5% for every 8 points of R-Value and each inch of thickness. So, the higher the R-Value or the thicker the panel is, the more you can expect to pay.
With this in mind, here is a breakdown of the average cost of 4′ x 8′ panels with different insulation levels:
Panel Thickness(Inches) | R-Value | Average Cost Per Square Foot | Average Cost Per 4′ x 8′ Panel |
4.6” | 16 | $7.50 per sq. ft. | $240/panel |
6.5” | 24 | $7.87 per sq. ft. | $252/panel |
8.2” | 32 | $8.26 per sq. ft. | $263/panel |
10.2” | 40 | $8.67 per sq. ft. | $276/panel |
12.25” | 48 | $9.10 per sq. ft. | $290/panel |
Generally speaking, when selecting SIP panels for a project, investing in higher-quality material that offers greater insulation is worthwhile. That way, it will help reduce heating and cooling costs down the road.
SIP Cost By House Size
The size of your home is directly related to the cost of your SIP installation. More panels will be needed for a larger, multi-story home, increasing the price.
The cost of R-16 insulation SIPs will typically range between $7 and $12 per square foot, depending on the panel size. A homeowner with a 2,000 sq. ft. home without a truss timber frame can expect to invest somewhere between $14,000 and $24,000 on the panels alone.
In a similar manner, R-30 SIPs for the roof may cost around $8.26 per square foot or $826 per roof square (100 square feet). You will likely require about 20 roofing squares for a 2,000 sq. ft. house, bringing your roof costs alone to approximately $16,500, without professional installation.
Here is a breakdown of SIP costs for several home sizes:
Home Size(Square Footage) | Average Cost for Wall Panels | Average Cost for Roof Panels | Total Cost (Materials Only) |
1,800 sq. ft. | $12,600 – $21,600 | $14,870 | $27,470 – $36,470 |
2,000 sq. ft. | $14,000 – $24,000 | $16,500 | $30,500 – $40,500 |
2,200 sq. ft. | $15,400 – $26,000 | $18,170 | $22,570 – $44,170 |
*Note: According to EnergyStar.gov, for optimal performance, a SIP project should use insulation panels with an R-value of at least R-16 for the walls and R-30 for the roof. For a higher-performance SIP house, an R-value of R-21 for walls and R-50 for the attic is recommended.
It’s important to bear in mind that these are only rough estimates of the cost of SIPs for different home sizes. Factors such as the size and configuration of your house, as well as local climate conditions, could cause the actual cost to vary significantly.
To get an accurate estimate, it’s best to consult a professional contractor or home builder, someone with experience in SIP construction, who will factor in all these considerations.
SIP Material Type
On average, the prices of SIPs range from $7 to $12 per square foot, depending on several factors, including the material and insulation type used. SIP panels are usually made from OSB (Oriented Strand Board) and rigid insulation material. They are typically used to create high-performance walls, roofs, or floors.
SIPs OSB
The OSB used for SIP panels, also called insulated panel skin, is one of the most popular components in the industry due to its durability and energy efficiency. The oriented strand boards are made of wood strands that have been chemically glued and compressed together to create a strong, lightweight material.
SIPs Rigid Insulation Material
Regarding rigid insulation material, polystyrene foam is the most widely used. This foam is often referred to as EPS (Expanded Polystyrene).
EPS is an excellent choice for insulation, providing a solid barrier with a high R-Value. However, if you’re looking for even better insulation, polyurethane foam (PUR) is the way to go. Polyurethane foam is more expensive than EPS but offers a higher R-Value.
Other insulation materials that can be used with SIP panels are:
- Polyisocyanurate
- Magnesium oxide
- Graphite
Labor Costs
SIPs are becoming increasingly popular for home construction and renovations, given their fast installation time, which reduces labor costs. Framing a home with SIPs takes around a week, whereas traditional stick framing can take much longer.
Since the SIP panels are assembled in a factory, much less labor is needed on-site during installation. Installing them can substantially reduce total construction time, resulting in savings on labor costs. Compared to other building methods, a homeowner can save up to 55% when using SIPs.
A carpenter and crew would typically charge an hourly fee to install SIPs, but factors such as the regional cost of labor, complexity of the structure, supplies, and tools needed can influence that rate. Generally, foundations, roofing, and windows will be the most expensive components to install. On average, a carpenter will charge anywhere from $50 to 100 per hour.
Related Services
In addition to the cost of SIPs, you may need other services like plumbing and electrical work for your building. While you can handle some of the tasks yourself, chances are you’re going to need a professional.
Furthermore, you might want to invest in additional energy-efficient measures like insulation, HVAC systems, or solar panels.
Electrical Wiring
If your new SIP building requires electrical wiring, you’ll want to hire an experienced electrician. They can help you design a cost-efficient setup from start to finish. They can also ensure your building is up-to-date with the latest safety and code requirements.
On average, an electrician will charge between $50 and $100 per hour. If you’re installing a complex system, get an estimate before the project begins so you won’t be faced with a larger bill than expected.
Plumbing Service
Another expense you should consider is plumbing services. For instance, you may need to install a new sink, toilet, or bathtub in your SIP building. It’s essential to use an insured and experienced plumber to ensure the job is done correctly. Plus, this professional can help you select the best fixtures for your building’s needs.
Plumbers typically charge between $45 and $150 per hour.
Other Insulation Options
Besides SIP panels, there are other ways to make your building energy-efficient. For example, you may want to add insulation to existing walls or attic space. Not only will new insulation reduce your utility bills, but it will improve the comfort of your building, too.
The cost of insulation is based on several factors, such as the type of insulation you choose and the labor required to install it. Generally, professional installation will cost between $1 and $5.65 per square foot, on average.
HVAC System Installation
When it comes to a SIP home project, you may also want to invest in a heating and cooling system. SIPs are high-performance walls, and they are excellent at retaining the temperature in your building. Therefore, there is no need to have a large or expensive HVAC system.
The price of an HVAC installation can range from $5,000 to $9,000, including the unit and labor fees.
Solar Panels
If you’re looking to reduce your energy bill even further, you can also install solar panels. This clean energy source allows you to produce electricity at a lower cost, in some cases reducing your energy costs by up to 90%. The price of a solar panel system will depend on the size and type of system you choose.
On average, a residential solar panel system will cost anywhere from $15,000 to $26,000 in total.
DIY Cost vs. Pro Cost
Pro Cost | $13,800 to $17,000 |
DIY Cost | $12,850 |
If you want to save yourself some money, you can always take on the task of installing SIP panels yourself. But be warned, while it’s a relatively simple process, there are some technical aspects. It is not recommended that you take this on unless you are quite handy and confident with DIY projects.
For bigger SIP projects, such as entire house installations, it’s probably best to consult a professional. They will be able to advise you on the right materials, appropriate site preparation, and the right design. However, if you’re just looking to get a few panels up as an addition, then read on.
Usually, the SIPs come with pre-installed connectors and other accessories that can help make DIY installation easier. For an 800 sq. ft. addition, you can easily DIY for about $12,850 on average. This will include the cost of panels, supporting materials, tools, and other supplies. Here is a basic breakdown of costs:
Item | Average Cost |
SIP Wall Panels | $7 per sq. ft. / $5,600 for 800 sq. ft. |
SIP Roof Panels | $8.26 per sq. ft. / $6,600 for 800 sq. ft. |
Circular Saw | $58 |
Hand saw | $10 |
Level | $35 |
Square | $13 |
Hammer | $18 |
Chisel/Stanley Knife | $15 |
Drill | $120 |
Tape Measure | $18 |
Ratchet Straps | $33 |
Pipe Clamps | $35 |
1-1/2″ Wood Bit | $35 |
Panel Lifting Equipment | $200 |
Protective Gloves | $18 |
Safety Goggles | $14 |
Hard Hat | $25 |
*Note: It is essential to read the manufacturer’s instructions carefully, as wrong installations can lead to damage and even further costs down the road. Additionally, you can void the warranty if something goes wrong.
When deciding whether you should DIY or hire a pro for your SIPs installation, the cost often plays a significant role. Professional installation for an 800 sq. ft. building takes around 2 to 3 days and can range from $13,800 to $17,000 on average. That’s roughly a few thousand dollars more than the DIY option.
However, if you don’t have the confidence or time to take this on yourself, hiring a pro is an excellent option, especially if you need a larger structure. The cost may be more, but it will save you time and hassle in the long run.
SIP Installation Cost by Location
The national average installation cost of SIP panels is around $7 to $12 per square foot, only for the panels. However, this can vary significantly depending on the location. Depending on where you are, the prices can differ due to availability and labor costs.
Moreover, different climates may influence the type of SIPs you need to install. For instance, in colder climates, better-insulated SIPs are necessary to keep the insulation and operating temperature up. That can drive the cost up since these types of panels are more expensive.
Contact a local insulation pro experienced with SIP installation to get an accurate quote for your project.
Pros and Cons of SIPs
SIP panels come with a lot of pros and cons. On the upside, they are lightweight, energy-efficient, and robust structures. They are also relatively easy to install since they come pre-fabricated, saving you time and money. On the downside, they tend to be more expensive than traditional construction materials.
The following table highlights the pros and cons of using SIPs for insulating your home:
Pros | Cons |
✔ Offer superior structural strength ✔ Provide super insulation to keep in the heat/cool air, meaning less energy is needed for HVAC systems ✔ Offer a tight seal with fewer joints to reduce air loss and increase air quality ✔ Can be adapted to any climate(tested in extreme temperatures) ✔ Easy to attach interior and exterior finishings ✔ Long-lasting durability (last up to 60 years if kept in dry conditions) ✔ Easier and faster to install than other building materials, cutting down on labor costs ✔ Keep pests at bay with their foam core construction ✔ Sustainable, as they have off-site fabrication & no waste on-site ✔ Environmentally friendly building solution | ✘ Susceptible to moisture damage ✘ Limited room for improvements ✘ Difficult to find experienced contractors ✘ Necessitates additional ventilation systems to avoid condensation and air stagnation ✘ Requires added insulation for an airtight seal ✘ Electrical wiring and plumbing installations present extra challenges ✘ High initial cost ✘ Lack of wall studs to attach heavy accessories ✘ Not suitable for flood zones or below-ground levels ✘ Must ensure the integrity of the bond between foam and board ✘ Expensive material costs, requiring a higher upfront investment |
FAQ
Yes, they do need ventilation. SIP panels are airtight, so it is essential to set up a proper ventilation system. This allows air to circulate and regulate the temperature over time.
The purpose of SIPs is to provide a high level of insulation, strength, and air-sealing. The interlocking SIP panels create a robust building envelope, making your home more air-tight, energy-efficient, and structurally sound.
Yes, SIPs can get wet, but they should not be saturated with water. If there is a leak or an area that constantly gets wet, you should take immediate steps to identify the cause of the leak and repair it as soon as possible.
The primary disadvantage of SIPs is the cost. While they offer many advantages, their upfront costs can be relatively high compared to traditional construction. In addition, modifications to the panels can be difficult once they are installed. You may need a professional for any significant alteration or installation.
SIPs are designed to last, with life cycles of up to 60 years or more. With good maintenance and proper installation, the lifespan of SIPs can exceed expectations.
Yes, SIPs can be used as a floor in certain conditions. The panels must be rated for flooring applications and are often structurally reinforced with additional materials. Plus, you must ensure the floor area is level, and the SIPs are correctly placed and secured beneath floor joists.
SIPs are constructed from polyurethane foam and are not technically fireproof. However, SIPs provide a good degree of protection from the heat and spread of fire. A SIP wall can significantly reduce the spread of fire compared to a traditional wooden structure, making them an excellent choice for fire safety in homes.
Final Thoughts
Generally, SIPs can range from $7 to $12 per square foot, depending on the type of materials used and the insulation desired. With SIPs, you can save money on energy bills, improve indoor air quality, and make your home more comfortable.
Additionally, SIPs offer an efficient solution for building with minimal waste, making them a great option for environmentally conscious homeowners. For an accurate installation cost, it is best to consult a local professional and discuss your project in detail.
Note: LawnStarter may get a referral fee for matching you with contractors in your area.
Main Image Credit: brizmaker / Canva Pro / License
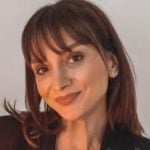